From Layout to Complete: The Full Light Weight Aluminum Casting Refine Demystified
In the world of production, the process of light weight aluminum spreading stands as a crucial approach that has actually sustained markets for years. Each action in this complex process, from the initial layout stage to the last finishing touches, plays an important function fit the outcome of the product. What really lies below the surface area of this process continues to be a mystery to several. By unraveling the complexities and clarifying the nuances associated with each stage, a deeper understanding of the art and science behind aluminum spreading arises. about aluminum casting. Stay tuned as we study the full aluminum casting procedure, uncovering the intricacies that transform raw materials right into refined items.
Creating the Casting Mold And Mildew
When launching the light weight aluminum spreading procedure, careful focus to creating the spreading mold is paramount for making sure the end product's honesty and quality. The casting mold offers as the foundation for the whole casting process, dictating the form, measurements, and surface finish of the eventual aluminum component.
To make an effective spreading mold, engineers need to take into consideration numerous elements such as the intricacy of the part, the kind of aluminum alloy being utilized, and the preferred homes of the end product. about aluminum casting. Computer-aided design (CAD) software program is frequently used to create in-depth schematics of the mold and mildew, permitting for specific personalization and optimization
Furthermore, the layout of the spreading mold directly impacts the efficiency and cost-effectiveness of the casting process. A well-designed mold minimizes product waste, minimizes the need for extensive post-casting machining, and improves overall manufacturing rate.
Melting and Putting Aluminum
With the design of the casting mold settled, the following vital action in the aluminum spreading procedure is the melting and putting of the light weight aluminum alloy. The process begins with loading the aluminum alloy into a heating system where it is warmed to its melting point, commonly around 660 ° C(1220 ° F) for light weight aluminum. Crucible furnaces, induction furnaces, or gas-fired reverberatory heaters are typically made use of for melting aluminum. As soon as the aluminum is molten, it is vital to preserve the temperature within a details variety to ensure the quality of the spreadings.
After the aluminum reaches the preferred consistency, it is time for pouring. The liquified aluminum is thoroughly transferred from the heater to the casting mold and mildew. This action calls for accuracy and control to avoid flaws in the end product. The pouring process should be carried out quickly to avoid early solidification and make certain the aluminum fills up the mold and mildew entirely. Appropriate putting strategies add considerably to the overall high quality of the last aluminum spreading.
Solidifying and Cooling Refine
Upon completion of the pouring process, the liquified aluminum changes into the cooling down and strengthening stage, a critical stage in the aluminum spreading process that directly impacts the last item's integrity and attributes. As the light weight aluminum begins to cool, its molecules organize themselves right into a strong type, progressively tackling the shape of the mold. The rate at which the light weight aluminum cools down is critical, as it influences the material's microstructure and mechanical residential properties. Quick air conditioning can cause a finer grain structure, improving the product's stamina, while slower air conditioning may bring about larger grain sizes, impacting the end product's ductility.
During this stage, it is crucial to regulate the cooling procedure meticulously to avoid problems such as porosity, shrinking, or internal stresses. Different air conditioning techniques, such as air cooling, water quenching, or regulated air conditioning chambers, can be used based on the specific requirements of click here now the casting (about aluminum casting). By checking and regulating the solidification and cooling process, producers can ensure the manufacturing of high-quality light weight aluminum castings with the wanted metallurgical and mechanical buildings
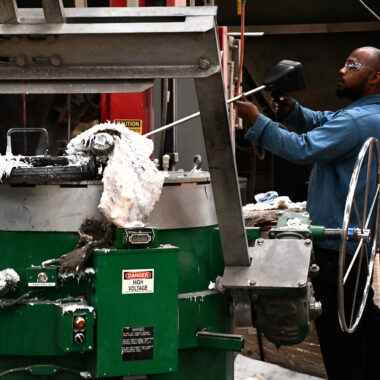
Removing the Final Spreading
As soon as the aluminum spreading has actually adequately solidified and cooled down in the mold and mildew, the next action in the process involves carefully getting rid of the final spreading. This action is important to make certain that the aluminum part is efficiently removed without any kind of damage or issues.
To get rid of the casting, the mold is opened, and the spreading is drawn out using different techniques depending upon the intricacy of the component and the mold and mildew layout. For easier shapes, the spreading can frequently be conveniently removed by hand or with easy devices. For even more elaborate layouts, added devices such as ejector pins, air blasts, or hydraulic systems might be required to facilitate the elimination procedure without causing any injury to the casting.
After the casting is effectively gotten rid of from the mold, any type of excess product such as entrances, joggers, or risers that were utilized during the spreading procedure are cut off. This step helps in achieving the last wanted look at more info form of the aluminum component prior to it undertakes any added ending up procedures.
Finishing and Quality Assessment
The final stage in the aluminum spreading procedure entails meticulous completing strategies and strenuous top quality examination procedures to make certain the stability and precision of the actors aluminum components. Finishing techniques such as grinding, fining sand, and shot blasting are made use of to get rid of any kind of excess product, smooth rough surfaces, and enhance the visual appeal of the end product. These procedures not just boost the look but also make sure that the parts meet the specified dimensional resistances and surface coating demands.
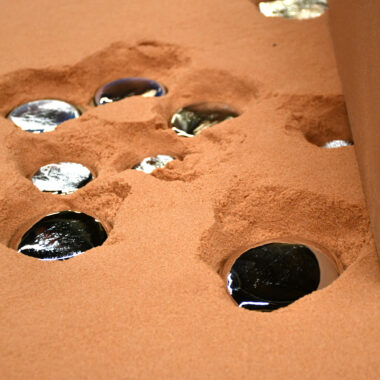
Final Thought
To conclude, the aluminum casting procedure entails designing the mold and mildew, melting and pouring light weight aluminum, strengthening and cooling the spreading, getting rid of the end product, and completed with a high quality examination. Each action is essential in guaranteeing the last item satisfies the preferred specifications. By understanding the whole process, makers can produce high-quality aluminum castings efficiently and efficiently.
Stay tuned as we study the complete aluminum spreading procedure, revealing the complexities that change raw materials into polished items.
With the style of the casting mold wrapped up, the next important action in the aluminum casting procedure is the melting and putting of the aluminum alloy.Upon completion of the putting process, the liquified light weight aluminum shifts into the cooling and strengthening stage, an important phase in the aluminum spreading process that directly affects the final product's stability and attributes.The final stage in the aluminum spreading procedure involves meticulous completing strategies and strenuous quality evaluation procedures to make sure the honesty and accuracy of the actors aluminum components.In conclusion, the light weight aluminum casting process includes making the mold, melting and pouring light weight aluminum, strengthening and cooling the casting, removing the final item, and completing with a quality evaluation.